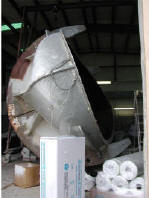 |
|
The solid fiberglass hull is laid up by
hand, mixing 5 gallons of red-tinted resin at a time, layering with
various woven cloth and matting. It takes 10 days to complete plus curing time.
The mold (1) is one piece, with a hinge down the middle for easy removal
later. The mold rocks back and forth in a cradle to facilitate fiber
glass application. Timbers (2) add strength and will be fiber glassed, and support the
sub floor. Notice the wide copper strapping running
along the sides for the SSB radio counterpoise.
The interior (3) is built completely within the boat - nothing is prefabbed.
This is light cherry wood
that will be oiled later. The deck is laid up separately as one solid
piece with balsa wood coring
in less-stress areas. Openings for hatches, ports, dorades, etc., are
then cut out according to the owner's specifications. The deck (4) is
lowered and the
bulkheads cut down to fit. Then massive amounts of 3M 5200 (permanent
adhesive) are applied to the hull surface, so as the deck is lowered into
place. The deck and aluminum toe rail are also fastened to the hull.
The deck, hull and all bulkheads are fiber glassed in place. It is
interesting to note that at this time NONE of the tankage, nor engine nor
generator, have been installed in the boat. This is intentional
- if it can all be put into the boat with the deck on, then it can be
removed, should it ever become necessary, with out tearing any out. Our 9,500 lbs. solid
lead keel (5) was forged in Seattle and trucked along with our mast.
Seventeen
J-bolts are used to secure the keel to the hull, in addition to 4 cases of
3M 5200 permanent adhesive. Our boat
then comes out of the production shop (6) on it's way to the paint shop.
It has been prepped already. |
|
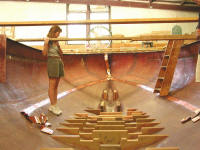 |